INŻYNIERIA MATERIAŁOWA 6/2016
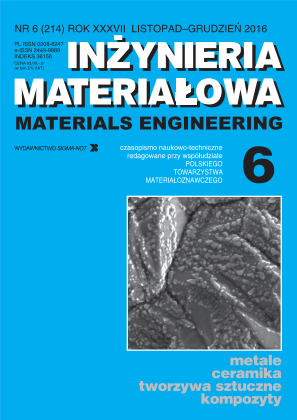
Cezary Senderowski, Tomasz Durejko, Dariusz Zasada, Wojciech Napadłek, Zbigniew Bojar
Structure and properties of the FeAl (HVOF, HVAF, DGS) coatings for power industry
DOI 10.15199/28.2016.6.1
Abstract
Recently, some systematic studies have been conducted on microstructural changes and material properties of B2 FeAl coatings sprayed by supersonic stream metallization in HVOF (High Velocity Oxygen Fuel), HVAF (High Velocity Air Fuel) and DGS (Detonation Gas Spraying) conditions. The present paper reports the results and analysis of HVOF, HVAF and DGS supersonic spraying on the structure and properties of Fe-Al type coatings obtained from spraying the Fe40Al0.05Zr at. % +50 ppm B intermetallic feedstock powder on a C45 steel substrate. A comprehensive study of the coating performances was conducted in relation to their material parameters by taking into account technological conditions affecting the formation of a structure in the ultrasonic spraying technologies. Analysis included chemical-phase composition inheritance, morphology of the grains, and porosity as well as oxidation of the coating material, hardness and abrasive resistance. These properties were analysed to determine if, Fe-Al coatings could be used as a potential material in the elements of gas turbines and boilers. Key words: Fe-Al type coatings, HVOF, HVAF, and DGS ultrasonic spraying technologies.1. INTRODUCTION The FeAl and Fe3Al-based iron aluminides are of interest as potential materials for hot structural applications, and they are promising substitutes for stainless steel and cast iron at room temperature, both as bulk materials and as coatings [1, 2]. Their promise is due to their good mechanical properties, relatively low density (5.56 g/ cm3 for the FeAl phase), excellent corrosion resistance in oxidizing and sulfurizing atmospheres (a result of their ability to form a highly protective Al2O3 scale), and low manufacturing cost [2, 3]. However, their use as bulk materials has been limited by their brittleness at room temperature and poor creep resistance [4]. The implementation of the Fe-Al type intermetallics as protective coatings can reduce these drawbacks. A[...]
Marek Opiela
Effects of Nb, Ti and V on recrystallization kinetics of austenite in HSLA steels
DOI 10.15199/28.2016.6.2
Abstract
The work presents research results of impact of Nb, Ti and V microadditions on recrystallization kinetics and microstructure of newly elaborated steels assigned for production of forged machine parts, using the method of thermomechanical treatment. The study was performed with the use of Gleeble 3800 simulator. In order to determine recrystallization kinetics of plastically deformed austenite, discontinuous compression tests of specimens were done with a given strain at the rate of 10 s-1, in a temperature range from 900 to 1100°C, with isothermal holding of samples between successive stages of deformation for 2 to 100 s. Recrystallization kinetics of plastically deformed austenite was described using the Johnson-Mehl-Avrami equation. Performed two-stages compression tests revealed that microadditions introduced into steel considerably influence the kinetics of static recrystallization. Determined time of total recrystallization of austenite, tR, in a temperature range from 1100°C to 900°C changes from 100 to 600 s and from 300 to 800 s — for the Ti-V steel and Ti-Nb-V steel, respectively. Executed hot compression tests will contribute to establishing conditions of forging with the method of thermomechanical treatment. Key words: HSLA steels, thermomechanical treatment, static recrystallization.1. INTRODUCTION HSLA-type (High Strength Low Alloy) microalloyed steels — containing up to 0.3% C and 2% Mn and microadditions with high chemical affinity to N and C, i.e. Nb, Ti and V in the amount of about 0.1%, and sometimes also slightly increased concentration of N and up to 0.005% of B, increasing hardenability — are particularly useful for production of forged parts with fine-grained microstructure using the method of thermomechanical processing. The interaction of microadditions in steel in a solid state depends on their state under conditions of performed plastic working. Microadditions dissolved in a solid solution rais[...]
Oskar Dziuba, Adam Kruk, Grzegorz Michta
Characterization of microstructure and mechanical properties of electron beam welded Allvac 718Plus butt welded joint
DOI 10.15199/28.2016.6.3
Abstract
Allvac 718Plus (718Plus) is a high strength, corrosion resistant commercial polycrystalline nickel-based superalloy developed by ATI ALLVAC over 10 years ago. 718Plus has been designed to fuse the most desired properties of Inconel 718 and Waspaloy, producing advantages of good mechanical properties, higher working temperature than Inconel 718, good fabricability and reasonable cost of production. 718Plus is strengthened by γʹ phase and other precipitates which are located mainly at grains boundaries. Compared to Inconel 718, 718Plus has increased concentration of Al, Ti and Co and decreased amount of Fe. Weldability of 718Plus is comparable to Inconel 718, thus there is a risk of intergranular microcracking in heat affected zone (HAZ). The test joint have been welded autogenously using electron beam at 120 kV accelerating voltage, 10 mA current and 78 cm/min welding speed. The microstructure of casted base material, heat affected zone (HAZ) and weld metal of electron beam welded 718Plus were investigated by means of light (LM) and scanning electron microscopy (SEM). SEM observations of welded joint microstructure were performed using secondary electrons (SEM-SE). SEM/EDS analysis were carried out. Both MC type carbides and Laves phase were observed in interdendritic regions of base material. The microstructure of heat affected zone was composed of γ matrix, γʹ phase and MC-type carbides, Laves phase and Laves/γ eutectic. In weld metal zone no γʹ precipitates were observed. The microhardness measurements have shown a decrease in weld metal and HAZ. It can be caused by an influence of the welding process thermal cycle. Key words: 718Plus, electron beam welding, SEM.1. INTRODUCTION Allvac 718Plus (718Plus) is a relatively recently developed nickelbased superalloy which properties lead to widespread potential of applications. This alloy belongs to a group of nickel-base superalloys strengthened by ordered[...]
Piotr Ledwig, Beata Dubiel
Preparation and preliminary study of the properties of electrophoretically depositied nc-TiO2 coatings on 316L steel
DOI 10.15199/28.2016.6.4
Abstract
TiO2 coatings on 316L steel were obtained by use of electrophoretic deposition (EPD) method. Potential zeta of nc-TiO2 particles in suspensions containing water and ethanol in different ratios was measured. Suspensions’ pH was stabilized by addition of acetic or citric acid and ammonia solution. Addition of citric acid in small amount decreased the zeta potential. Optimal suspensions’ parameters for cathodophoretic and anodophoretic deposition were selected based on the results of zeta potential measurements versus pH for suspensions with different water-ethanol concentration. For the chosen suspensions the rate of TiO2 deposition was measured. Coatings’ cohesion was improved by sintering or addition of biopolymer (chitosan) into suspension. The microstructure of coatings was examined by scanning electron microscopy. The roughness and thickness of the coatings were measured by optical profilometer. The corrosion resistance in Ringer’s solution was examined by use of polarization curves. The corrosion resistance of coated steel was higher than that of uncoated one. For sintered coatings the corrosion currents were lower, but the passive area was larger for not sintered ones. The contact angle of the coatings was measured using a sitting drop method and superhydrophilic properties of TiO2 coatings were confirmed. Manufactured coatings may be potentially used as self-cleaning materials. Additionally, TiO2 coatings improve corrosion resistance of steel and exhibit good bactericidal properties. These characteristics may make this sort of materials potentially useful also for medical purposes. Key words: TiO2 coatings, electrophoretic deposition, 316L steel, zeta potential measurements, superhydrophilic coating.1. INTRODUCTION Stainless steel is commonly used in many areas, e.g. marine systems, nuclear, chemical, food, construction industries and biomedical purposes [1÷3]. A wide range of industrial applications is possible [...]
Zofia Buczko, Marianna Gniadek, Klaudia Olkowicz, Waldemar Okurowski
Copper/nanodiamond composite coatings obtained by electrochemical deposition
DOI 10.15199/28.2016.6.5
Abstract
Copper composite coatings with nanodiamond particles were electrochemically deposited. Depositions were made on copper sheet basis in acid sulphate solutions with and without organic additives. The studies indicate the possibility of electrochemical deposition of composite Cu/diamond coatings and the coating properties depend on solutions composition. The concentration of the diamond preparation in process electrolyte solutions was about 0.5 g/dm3. The composites surface morphology was investigated by SEM microscopy and chemical composition with EDS microanalysis. Concentrations of diamond particles in samples surfaces were evaluated by ImageJ computer analysis. Hardness of coatings were measured by Vicker’s method. Key words: composite coatings, copper/nanodiamond composites, electron microscopy, EDS analysis, hardness measurements.1. INTRODUCTION Metal matrix composites with incorporated disperse phases are intensively investigated. The research is aimed at the production of materials having improved mechanical, tribological, electrical, thermal, and other properties. An important area of application are power electronics devices. The evolution of devices in a miniaturization direction causes problem of heat dissipation of integrated circuits based on semiconductors commonly used, such as Si, SiC and GaAs, and new one like GaN [1]. New electronic devices would be implemented in telecommunications, aerospace, military equipment and other industries [2÷7]. Copper is attractive as a matrix material because of good electrical conductivity, but also very good mechanical properties, like plasticity. There are attempts to incorporate into Cu matrix additional phase of carbon particles, also like micro- and nanodimensional diamonds [8]. Advantageous properties for this kind of material is its large thermal conductivity and low thermal expansion coefficient. Diamond is also hardest known material. Obtaining a composite material with di[...]
Agata Sotniczuk, Marta Zwolińska, Maria Sozańska, Andrzej Królikowski, Halina Garbacz
Nanostructure effect on the electrochemical response of titanium
DOI 10.15199/28.2016.6.6
Abstract
The purpose of this work was to investigate the influence of nanostructure on titanium corrosion resistance in physiological saline (0.9% NaCl). In order to obtain the nanostructure the titanium rod was processed through multiple hydrostatic extrusion (HE). Corrosion tests included electrochemical impedance (EIS) and potentiodynamic (PD) measurements. EIS tests were performed after 2 and 24 hours of immersion in 0.9% NaCl. Potentiodynamic measurements were carried out immediately after the last impedance test. Profilometric examination was used to check whether the samples were equally prepared for corrosion measurements. After corrosion tests a scanning electron microscope (SEM) was used to characterize the morphology of the surface. Corrosion tests revealed the positive influence of nanostructure on titanium corrosion resistance. Moreover, the differences observed were larger in the case of a shorter time of immersion in physiological saline. Hence, it might be surmised that the rate of the passivation process depends on titanium grain size. The microscopic characterization of the surfaces of samples after the corrosion test indicated differences in the surface morphology. The passive film formed on the nanocrystalline sample was more compact and homogenous than on the microcrystalline one. The different number of structural defects in micro- and nanocrystalline titanium might be the reason for the observed phenomena. Due to their higher energy, structural defects could be preferential sites for the nucleation of passive layers. Consequently, the rate of passivation should be higher for nanocrystalline materials. Furthermore, the high volume fraction of structural defects also explained the existence of more tight and uniform passive layer on the nanocrystalline titanium. Good corrosion resistance in physiological saline means that nanotitanium could be an attractive material for biomedical applications. Key words: corrosion, nanostructured [...]
Magdalena Szklarska, Bożena Łosiewicz, Grzegorz Dercz, Danuta Stróż
AC impedance study of the corrosion resistance of the passivated Ti15Mo implant alloy in physiological saline solution
DOI 10.15199/28.2016.6.7
Abstract
The object of this work was the self-passivated Ti-15 wt % Mo implant alloy subjected to anodic oxidation in 1 M acetic acid aqueous solution at 5 V for 1 h. In order to thicken the oxide film a superior biocompatibility and corrosion resistance of the anodized implant was achieved. Surface of the tested alloy before and after anodizing was characterized using X-ray diffraction analysis (XRD), scanning electron microscopy (SEM), energy dispersive X-ray spectroscopy (EDS) and profilometry. Electrochemical impedance spectroscopy (EIS) measurements revealed a passive behaviour of the alloy under the experimental conditions. The bilayer oxide film consists of a porous outer layer (6.7±1.0 nm) and a thin, solid inner-barrier layer (1.4±0.3 nm). The obtained film is three times thicker than the oxide layer formed by self-passivation. The electrochemical studies in physiological saline solution (PSS) at 37°C showed that the anodic oxidation improved the corrosion resistance of the Ti15Mo alloy. No pitting corrosion was detected in anodic polarization measurements up to 9.5 V due to the presence of the barrier oxide layer on the alloy surface and phase composition of the examined alloy which contained only β-Ti phase. Key words: Ti15Mo alloy, anodization, oxide layer, corrosion resistance, EIS.1. INTRODUCTION In recent years titanium and its alloys were found to be very popular biomaterials for medical applications due to their excellent mechanical properties, high biocompatibility and good corrosion resistance [1]. Nowadays, toxic metals present in medical titanium alloy are replaced by neutral and non-harmful ones for human body. Among these materials, Ti15Mo alloys can be some examples. Allergenic and carcinogenic elements such as Ni, Al and V have been replaced by a biocompatible molybdenum [2]. Addition of Mo increases the corrosion resistance simultaneously reducing the elastic modulus [3]. If the Mo content is higher than 10[...]
Łukasz Frocisz, Janusz Krawczyk, Rafał Dziurka, Kamil Górecki, Grzegorz Cios, Łukasz Gondek
Microstructure and phase composition characterization of a Ti–Al intermetallic alloy
DOI 10.15199/28.2016.6.8
Abstract
Intermetallic Ti-Al alloys are characterized by the unique set of properties which makes these alloys a prospective material for the energy, automotive and aviation industries. The mechanical properties of a intermetallic alloys are strictly related to the microstructure. The refinement of the microstructure can be obtained by the manufacturing process, alloying additions and heat treatment. Microstructure characterization and knowledge about phase transformation mechanisms and their temperature ranges allows to change properties of the bulk material. The aim of this study was the microstructure and phase composition characterization of intermetallic Ti48Al2Cr2Nb alloy. The microstructure was examined using the light and scanning electron microscopy. Identification of phases and their temperature stability were determined by X-ray diffraction, differential dilatometry and calorimetry investigation. The oxidation process was determined by high temperature X-ray diffraction and the thermogravimetric method. The alloy after annealing has a duplex microstructure with precipitations of α2 phase in the γ matrix. Dilatometry and calorimetry allowed us to define the stability of each phase. At first the enriched in chromium α2 phase dissolved, after that the regions depleted in chromium were transformed, and above 775°C the microstructure was only the γ phase. Gamma phase was transformed above 1100°C, the end of transformation γ → α was evaluated as 1250°C. The oxidation investigations allowed us to show that the oxidation process started at 700°C by the oxide layer formation, which was stable till 900°C. Above this temperature the oxide layer started to grow. Key words: intermetallic alloy, microstructure, phase composition, Ti48Al2Cr2Nb, titanium alloy.1. INTRODUCTION Titanium intermetallic alloys due to their unique properties could find possible applications in a wide range of the industries, especially when th[...]
Michał Kulka, Dominika Panfil, Jerzy Michalski, Piotr Wach
Effect of laser heat treatment parameters on the microstructure and hardness of gas-nitrided layers
DOI 10.15199/28.2016.6.9
Abstract
Nitriding is commonly used method of thermochemical treatment in order to produce surface layers of improved hardness and wear resistance. Using a gas nitriding with changeable nitriding potential, a nitrogen concentration at the surface could be controlled, influencing the phase composition and the growth kinetics of the layer. In this study, the hybrid surface treatment was applied. It consisted in gas nitriding and laser heat treatment (LHT) of 42CrMo4 steel. Two nitriding processes were carried out using changeable nitriding potential. Parameters on first process were as follows: temperature 570°C (843 K), time 4 h. The second process was performed at lower temperature 520°C (793 K) and longer duration 10 h. This resulted in various depths of the compound zone at the surface (20 and 8 μm, respectively). Next, the nitrided layers were laser heat-treated using TRUMPF TLF 2600 Turbo CO2 laser. Laser tracks were arranged as the single tracks with various scanning rates (vl = 2.88 m/min and vl = 3.84 m/min). The laser beam power (P) ranged from 0.26 to 0.91 kW. The effects of the depth of compound zone as well as LHT parameters on the microstructure, dimensions and microhardness of laser tracks were analysed. In the majority of the produced laser tracks, remelted (MZ) and heat-affected (HAZ) zones were easily identified. Different microstructure was visible at low laser beam power (0.26 kW). The dimensions of MZ were limited, whereas the HAZ was clearly observed. The compound zone was still visible at the surface. Only the porous ε nitrides were slightly melted. Hardness increased significantly after LHT with complete and partial remelting of compound zone. Laser beam power and scanning rate influenced the depth and width of MZ and HAZ, so the thickness of hardened zone. The greater laser beam power or the smaller scanning rate, the larger hardened zone was observed. Key words: gas nitriding, laser heat treatment, microstructure, hard[...]
Jerzy Pacyna, Rafał Dziurka, Małgorzata Grudzień
Influence of niobium on the structure and properties of the matrix of high-speed steel with nickel
DOI 10.15199/28.2016.6.10
Abstract
The following paper investigates two model alloys simulating the quenched matrix of high-speed steels with an addition of 1.5% Ni, which was enriched with 1% and 2% of Nb to increase abrasion resistance. Based on the alloys’ composition comprising of W, Mo, V and Cr, the simulations of the quenched matrix of the high-speed steels indicate sufficiently high hardenability. The purpose of increasing the nickel content in the composition of such alloys was to increase their crack resistance, whereas the addition of the strongly carbide-forming niobium in amounts of 1% and 2%, balanced by an additional carbon content, was aimed at increasing the abrasion resistance of these steels. The authors of the above mentioned chemical composition concept expect that these types of alloys will be used in the production of tools (rolls) designed for the rolling of metallurgical products which are difficult to produce (flat bars, channel bars and tee bars). The quenching temperature of both alloys was optimised on the base of the so called quenching series. The accurate CCT diagrams and the tempering series for revealing the secondary hardness effect were also performed for these alloys. All investigation stages were accurately documented by metallographic tests. Key words: metallic alloys, high-speed steel, phase transformations, dilatometric investigation, CCT diagrams.1. INTRODUCTION Intensive investigations of high-speed steels and their quenched matrix were carried out at the AGH in Krakow, during the 1970s [1]. The influence of the most important alloying additions to this steel group was determined by, among other things, the influence of the W/Mo ratio content on hardness, bending strength, crack resistance (by KIc method), prior austenite grain size, retained austenite fraction and tempering. The basic alloy of those investigations constituted the matrix of quenched steel HS6-5-2, whose chemical composition: 0.5% C, 2.0% W, 2.8÷3.0% Mo, 4.5÷[...]
Michał Żelechower, Elwira Czerska, Elżbieta Augustyn
Erbium/Ytterbium co-doped oxyfluoride glass-ceramics - promising candidate for fiber lasers and optical amplifiers at 1550 nm
DOI 10.15199/28.2016.6.11
Abstract
The manufacturing of the erbium/ytterbium co-doped oxyfluoride glass-ceramics optical fiber was discussed on the background of literature review and own achievements. The role of erbium ions as NIR emitters as well as ytterbium ions in the process of stimulated emission has been explained and illustrated by several figures both from the literature and the author’s results. Glass-ceramics material advantage over glassy fibers was also considered and proved by several plots and images. The relations between the g-c materials and their optical features have been illustrated by results of SEM/TEM imaging, X-ray spectra, XRD and SAED patterns, thermal analysis (DTA/DSC) and a corresponding absorption/emission NIR spectra. Key words: fiber laser, rare earth ions, glass-ceramics, edfa, nanocrystals.1. INTRODUCTION A chance to establish the long distance waveguide communications appeared in early seventies due to super pure low-loss fused silica glass optical fibers (about 90% of SiO2) fabrication. Since silica fiber attenuation is wavelength dependent (Fig. 1), the term “optical fiber communication window" has been introduced and currently the third window (1550 nm) is utilized for long distance cables with attenuation better than 0.3 dB/km. In traditional optical communication systems a signal regeneration was achieved in the form of optoelectronic repeaters located every 20÷50 km of the fiber cable (Fig. 2). They used three steps of signal regeneration: optical-to-electric conversion, amplification, and shaping and finally electric-to-optical conversion. Currently, several more sophisticated solutions (optical amplifiers without signal conversion) have been invented (EDFA - Erbium Doped Fiber Amplifier, SOA - Semiconductor Optical Amplifier, RFA - Raman Fiber Amplifier) and of them the EDFA amplifiers seem to be most common. Their heart is silica (plus GeO2) glass erbium doped optical fiber (Fig. 3). Actually, the EDFA amplif[...]
INŻYNIERIA MATERIAŁOWA 5/2016

Grzegorz Cempura, Bogdan Rutkowski, Jakub Jelita Rydel, Krzysztof Cieszyński, Aleksandra Czyrska-Filemonowicz
Microstructural evolution of HR6W alloy during ageing at high temperature
DOI 10.15199/28.2016.5.1
Abstract
The HR6W alloy (23Cr40Ni30Fe7WTiNb) is a candidate for boiler components of advanced ultra-supercricical (A-USC) conventional power plants. The influence of isothermal ageing at 700°C and 900°C for up to 110 hours on the microstructure of HR6W alloy was investigated in detail by advanced scanning and transmission electron microscopy methods. The results show that, beside primary MX carbonitrides, the M23C6 and Laves phase, Fe2W, were precipitated in the austenitic matrix. Their size and spatial distribution depend on ageing conditions. Microstructure changes influenced the hardness of the investigated alloy. Key words: HR6W, microstructure, scanning electron microscopy (SEM), transmission electron microscopy (TEM), steam power plant (SPP).1. INTRODUCTION The HR6W is Ni-Fe based alloy produced by Nippon Steel & Sumitomo Metal Corporation with a nominal composition of 23Cr40Ni30Fe7WTiNb designed for tubing, especially for superheaters and reheaters coils and for thick-walled elements of boilers. The HR6W alloy is the candidate for advanced ultra-supercritical (A-USC) boiler pressure elements owing to its superior creep and oxidation resistance at high temperature [1÷4]. The aim of the study was to examine a stability of the HR6W alloy microstructure during ageing at 700°C and 900°C affecting its mechanical properties during service in the power plant. The highest ageing temperature was chosen based on phase equilibrium diagrams and corresponds to operating temperature of 670°C for up to 200 000 hours service for HR6W alloy [5]. 2. MATERIAL AND EXPERIMENTAL DETAILS The chemical composition of the investigated HR6W alloy and standard requirements for HR6W alloy are presented in the Table 1. The alloy was delivered as the tube with outside diameter of 38 mm and wall thickness of 8.8 mm. The as-received alloy was solution treated at temperature range of 1190÷1250°C followed by fast cooling [6]; the exact parameters of heat treatment were[...]
Agnieszka Szczotok
Influence of variable casting wall thickness and shell mold material and its thermal properties on secondary dendrite arm spacing in IN 713C superalloy castings
DOI 10.15199/28.2016.5.2
Abstract
1. INTRODUCTION Different casting parameters can change the microstructure and mechanical properties of nickel-based superalloys. Kostić, Golubović, and Valčić [1] described how temperature gradient, crystal growth rate, and concentration of the alloying elements influence the microstructure and physical properties of the material. Polycrystalline and single-crystal nickel-based superalloy castings exhibit a dendritic structure that is the most common growth morphology during the solidification of metals and alloys. Each dendrite consists of primary arms (PDAs), secondary arms (SDAs), and even tertiary arms (TDAs). The secondary dendrite arm spacing (SDAS), which is defined as the distance between the protruding adjacent secondary arms of a dendrite (Fig. 1), has been recently used to describe the metallurgical structure of cast materials. It is well known that variations in the cooling rates during solidification can give rise to the various morphologies of the as-cast structures; these then lead to variations in their mechanical properties. Values of primary dendrite arm spacings (PDAS) and secondary dendrite arm spacings (SDAS) under controlled conditions can be used to predict the microstructure and properties of the castings and to develop a theoretical foundation for the control of microstructure and properties and the optimization of the industrial processing parameters. This has motivated many studies of PDAS and SDAS in dendritic structures [2÷6]. Along with the other microstructural parameters, PDAS and SDAS have a strong effect on the mechanical properties of Ni-based superalloys [5]. Over the past several decades, extensive experimental studies of PDAS have been carried out and a number of theoretical models have been developed [7÷11]. The relationships between the solidification processing parameters and PDAS have been established experimentally and theoretically [12]. Numerous studies of SDAS and dendrite growth [...]
Bogdan Rutkowski, Aleksander Gil, Wiktoria Ratuszek, Barbara Woźnik, Aleksandra Czyrska-Filemonowicz
The microstructure of the Sanicro 25 steel after steam oxidation studied by advanced electron microscopy and spectroscopy methods
DOI 10.15199/28.2016.5.3
Abstract
Increase of the coal fired power plants efficiency is inseparable with an increase of the steam conditions. Currently used 9÷12% Cr steels are not able to withstand pressure of 30 MPa at 700°C for a long time due to their microstructure instability leading to fast damage. Development of new Fe-based materials able to work under advanced ultra-supercritical (A-USC) conditions for a long time is the key of importance. Present paper deals with a microstructure of the prospective, 22% Cr austenitic steel, Sanicro 25, heat treated or oxidized in water vapour at 700°C. Detailed characterization of the steel was performed using X-ray diffractometry as well as scanning and transmission electron microscopy techniques. Investigation led to establish the effect of temperature and water vapour environment on the microstructure stability of this modern austenitic steel. The results showed that the microstructure of the aged steel consists of M23C6 and Laves phase precipitated on the grain boundaries as well as ε-Cu, NbN, M23C6 and Z-phase precipitated within the grains. After oxidation at 700°C up to 5000 h in water vapour, Sanicro 25 developed a thin protective oxide scale at the surface, consisting mainly of Cr2O3 plates, characteristic for steels oxidation in vapour. Key words: Sanicro 25, TEM, oxidation, water vapour, A-USC.1. INTRODUCTION Nowadays, environmental protection takes a particular significance due to high emission of CO2, which is one of the major greenhouse gases causing global warming. Major CO2 sources are coal-fired power plants, therefore particular efforts are made in order to decrease the CO2 emission by increasing the thermal efficiency of the power plants due to enhancing temperature and pressure of the steam to 700°C and 30 MPa, respectively. Such change, however, has strong impact on the microstructure stability and lifetime of the currently used materials. Commonly used 9÷12% Cr steels are not suitable to operate at t[...]
Łukasz Maj, Jerzy Morgiel, Maciej Szlezynger, Małgorzata Pomorska
Transformation of Ti/Al multilayers to the Ti3Al phase aimed at bonding of titanium alloys
DOI 10.15199/28.2016.5.4
Abstract
The freestanding Ti/Al multilayer (with 3:1 the chemical composition ratio) was applied to bond the parts from Ti-6Al-4V alloy. The as-deposited multilayer and the joint obtained with it were characterized with the use of transmission electron microscopy (TEM) method including selected area electron diffraction (SAED) and energy dispersive X-ray spectroscopy (EDS). It was observed that the annealing at 800°C for 1 h in vacuum of 1 Pa helped to transform Ti/Al multilayer into fine grains (grain size < 1 μm) of Ti3Al acting as a filler material between pieces of Ti-6Al-4V. The resulting joint shows generally good connection with the presence of small porosity both at the filler material/Ti-6Al-4V base material interface (larger) and on the Ti-6Al-4V side (smaller). Additionally, near surface zone of the joint, the parts were strongly depleted of aluminium. Key words: diffusion bonding, Ti/Al multilayers, Ti-6Al-4V alloys, TEM, EDS.1. INTRODUCTION Heating of Ti/Al multilayers could result in the formation of various titanium aluminides, such as Al3Ti, Ti3Al or TiAl. Due to negative enthalpy of mixing their formation is accompanied by a strong exothermic effect [1, 2]. The type of a final product depends on the bilayer thickness ratio, i.e. averaged multilayer chemical composition. However, slow heating of the whole multilayer causes that the reaction is controlled through a solid state diffusion (SSD) across neighboring interfaces being an example of one of phase transformations in solid state [3]. The level and extent of the local intermixing, both increasing with lowering of the multilayer period, decides on the phase precipitation sequence taking place during this process [4]. Fast local temperature rise leads to a reaction known as self-propagating hightemperature synthesis (SHS) occurring along the multilayers in the form of roughly planar front. In Ti/Al multilayers it is accompanied by melting of aluminium layers and conseque[...]
Grażyna Balcerowska-Czerniak, Adam Dittmar-Wituski, Tomasz Hiller, Antoni Bukaluk
Efficiency of chemometric methodology for characterization of In/CuPc films on HOPG and InSb based on ultraviolet photoelectron spectra
DOI 10.15199/28.2016.5.5
Abstract
Photoemission spectroscopy offers the possibility to study on the interface formation of copper phthalocyanine exposed to indium. In this paper, we demonstrate the potential of using chemometric treatment in the characterization of In/CuPc films on HOPG and InSb substrates based on ultraviolet photoelectron spectra (UPS). The main advantage of using chemometric methods is that there is no need to construct of line intensities models to gain valuable information. The experimental data sets have a bilinear mathematical structure and, therefore, they can be subjected to principal component analysis (PCA). The results of PCA showed that the principal component loadings provide useful information about the changes in the line intensities and the peak positions. The obtained graphical models of data, in a simple way, enabled the determination of new supplementary information concerning the role of the individual chemical compounds in terms of In/CuPc interface formation. Moreover, chemometric classification method such as cluster analysis (CA) allowed identifying the subgroups of samples according to a specific property of formed components. Key words: metal-organic interfaces, copper phthalocyanine, chemometrics.1. INTRODUCTION Among the wide range of metal-organic semiconductor interfaces which has been reported in the literature, the phthalocyanines family has received a lot of attention due to their biological significance, catalytic properties and technological interest. Copper phthalocyanine often referred to as CuPc, is well known material for their semiconducting behaviour. The nature of its chemical and electronic structure has been the topic of numerous research in recent years [1÷4]. A great deal of the attention has been paid for studying interface formation at deposition of different metals on CuPc thin films, due to their promising optical and electrical properties [5÷8]. Several papers refer to interface formation between copper[...]
Justyna Zygmuntowicz, Aleksandra Miazga, Waldemar Kaszuwara, Remigiusz Nowacki, Katarzyna Konopka
Processing and characterization of ceramic–metal composites obtained by centrifugal slip casting
DOI 10.15199/28.2016.5.6
Abstract
Hollow shaped cylinders have been prepared from alumina-nickel composites with a gradient distribution of Ni by centrifugal slip casting method from water based slurries containing Al2O3 and Ni powders, and sintered at 1400°C in reducing N2/H2 atmosphere. No new phases like nickel aluminate spinel were revealed by X-ray diffraction in the Al2O3-Ni graded composites. Scanning electron microscopy (SEM) observations showed the presence of gradient distribution of Ni particles within the cross-section of the samples. Hardness tests confirmed that the nickel particles are distributed in the composite in a gradient way. Key words: composites, Al2O3-Ni, centrifugal slip casting.1. INTRODUCTION Since the 80’s of the XX century, the ceramic-metal composites aroused considerable interest primarily due to their properties [1]. Ceramic-metal composites are a group of materials that combine the following properties: high hardness, heat resistance and corrosion resistance [2, 3]. With the addition of the metallic phase we can obtain a noticeable improvement in fracture toughness, which allows a wider range of application than in case of monolithic ceramic materials. The ceramic matrix composites may find application such as ceramic gas turbine [4], a turbine blade [5] and others. The main mechanisms responsible for improvement of fracture toughness of the ceramic matrix composites reinforced with metal particles are: crack deflection path by metal particles, crack bridging, dislocation mechanism and in some cases phase transformation [1, 6÷9]. The strength of the interface between a ceramic matrix and a metal particles has got a crucial influence on the occurring type of mechanism [1]. The ceramic-metal composites may be produced by various methods such as infiltration of porous ceramics by liquid metal [10], slip casting method [11] and others. In this article the Al2O3-Ni composites produced by centrifugal slip casting (CSC) method were[...]
Adrian Mróz, Dariusz Garbiec, Jarosław Jakubowicz, Łukasz Łapaj, Agnieszka Wielowiejska-Giertuga, Monika Gierzyńska-Dolna
Effect of manufacturing technology on tribological properties of Co28Cr6Mo alloy
DOI 10.15199/28.2016.5.7
Abstract
The physical, chemical, mechanical properties of alloys used in endoprosthesis components in the osteoarticular system or dental implants depend not only on the chemical composition, but also on the applied production technology. The article presents the results of friction and wear testing of samples produced by selective laser melting and spark plasma sintering of the ASTM F75 alloy powder (Co28Cr6Mo alloy). As reference material, an ASTM F1537 LC rod was used from which samples were prepared by machining. The friction and wear tests were conducted by means of a tribological tester with a block-ring tribosystem. The tests were performed without lubricating fluid at ambient temperature. The test results constituted a comparison of the frictional resistance in contact with bearing steel 100Cr6 as well as a comparison of the wear values depending on the given friction pair load as a function of sliding distance. Analysis of the wear mechanism of the test materials was based on microscopic observation of the friction surfaces, chemical composition analysis of the surfaces using energy dispersive X-ray spectroscopy as well as roughness measurements. For the friction pair involving the reference sample, the friction coefficient was characterized by a constant value of about 0.40 regardless of the load or travelled sliding distance. In the case of the samples greater frictional resistance was found. The friction coefficient for the friction pairs involving samples produced using the technology of selective laser melting and spark plasma sintering varied in the range 0.50 to 0.62 and from 0.70 to 0.74. Based on the obtained results of weight loss, it was calculated that the reference material sample was characterized by the smallest wear coefficient, while the largest was demonstrated by samples produced by spark plasma sintering. Microscopic observations showed that regardless of the employed technology to produce the samples, the dominant type of w[...]
Piotr Maj, Jarosław Mizera, Tomasz Pieja, Tadeusz Gancarczyk, Stanisław Dudek, Jan Sieniawski
The development of metal spinning - new opportunities and possibilities
DOI 10.15199/28.2016.5.8
Abstract
Metal spinning is a forming process known since ancient times. However on an industrial scale it is used from the beginning of the twentieth century. Thanks to the technology it is possible to obtain complex axisymmetric shapes with excellent mechanical and surface properties. It is a promising forming technology that is becoming more popular especially in advanced application such as aircraft industry. It has a lot of advantages; among others it allows shaping the material properties in a larger extent than the commonly used metalworking methods. Furthermore since 2001 for the first time laser assisted heating was used in the process enhancing it even further. The article presents the metal spinning technology and its current developments. Additional practical aspects were described in the research and underlined by the authors. The last paragraph concerns sample results of mechanical tests carried out on the fabricated elements that show the possible application of the method particularly in the aircraft industry. The hardness of the cold formed element increased more than twice after 70% reduction in cross section in a single tool movement. In the longer term perspective laser assisted metal spinning could reduce the costs and improve the properties of the currently used aircraft engine parts by eliminating intermediate annealing. Key words: metal spinning, shear forming, aircraft materials, Inconel 625.1. INTRODUCTION The process for metal spinning has been known since ancient times. In its kinetics, the process is derived from craft techniques used in pottery. The rotary element is formed by the pressure of the tool (rollers) rotating around its own axis, reproducing the final shape of the product on the mandrels (rotating form). Processing is continuous; its advantage is the possibility of forming complex axisymmetric shapes. Additionally, a large number of control parameters allow for a wide scope in controlling not only the dimensi[...]
Mateusz Szymański, Bartosz Michalski, Marcin Leonowicz, Zbigniew Miazga
Pressure effect on hydrogen absorption by Nd-Fe-B magnets during HD and HDDR
DOI 10.15199/28.2016.5.9
Abstract
Scrap, sintered Nd-Fe-B magnets were subjected to hydrogen treatments of Hydrogen Decrepitation (HD) and Hydrogenation-Disproportion-Desorption and Recombination (HDDR) route. In HD treatments, increasing hydrogen pressure from 100 kPa up to 200 kPa at room temperature, does not affect particles size distribution but accelerates the reaction by decreasing the incubation time. In this study a faster HD process is reported when fresh materials are provided compared to one week stored ones. As part of the exothermic nature of the HD process, the increment of temperature was registered. The temperature rise was slightly higher for the fresh material (close to 2°C) comparing with the one week stored material (around 1.5°C). Hydrogen absorption was analysed during the HDDR process carried out at 850°C under three hydrogen pressures: 30, 100 and 200 kPa. For 30 kPa, due to hydrogen consumption, additional refilling was necessary, while other tested pressures were high enough to avoid additional refilling during the HDDR. Key words: hydrogen decrepitation, hydrogenation-disproportionation-desorption and recombination, hydrogen absorption.1. INTRODUCTION Recovery of rare earth metals is forced by a huge demand for these critical materials strongly requested by the high-tech industry [1]. Electronic devices, modern medicine, automotive industry, as well as green energy sectors are the biggest receivers of these unique and precious metals. Some of the products, with high demand in these areas, are high performance magnets made of rare earth elements. Hydrogen-assisted recycling treatments are currently under investigation for such magnetic materials [2, 3]. As an example, Hydrogen Decrepitation (HD), discovered by Harris et al. [4], allows for crushing of bulk pieces of Nd-Fe-B ingots into hydride powder. This is caused by an increase of volume in the rare earth metal lattice due to absorption of hydrogen. In magnets, hydrogen is absorbed mostly b[...]
Dominik Kukla, Paweł Grzywna, Mateusz Kopeć, Zbigniew Kowalewski
Assessment of hardened layer thickness for 40HNMA steel using eddy current method
DOI 10.15199/28.2016.5.10
Abstract
Materials and semi-manufactured products for aviation equipment are usually subjected to increasingly rigorous demands for the quality control. In many cases, like hardened or carburized wheels or rollers assembled in the gear motors, the control procedures enforce necessity of the selective testing of details coming from production lines using destructive techniques. The main aim of diagnostic investigations carrying out on series of final products is to assess qualitatively and quantitatively the layers obtained due to carburizing and induction hardening. Unfortunately, such processes increase the fabrication costs significantly, especially in the case of complex manufacturing technology applied and small-lot production as well. In order to reduce them the attempts for application of non-destructive testing methods are taken for evaluation of either the layers quality or the products subjected to surface treatments. This paper presents the eddy currents method used for the thickness evaluation of the carburized and induction-hardened layers on the basis of the impedance signal variation. The signal was obtained as a result of the so-called ‘lift off’ effect. A methodology for the quantitative thickness evaluation of the carburized and induction-hardened layers has been elaborated under a range of technological parameters. The measurements ranges were defined in the framework of which an identification of the hardened layer was possible using the commercial defectoscope and reference specimens of the fixed thickness. Tests were carried out on specimens made of the ASM6414 steel and subjected subsequently to carburization and induction hardening. The impedance parameters were measured for selected values of frequency. The results were verified on the basis of metallographic investigations as well as the microhardness measurements captured in the form of profiles taken from specimens’ cross-sections of different layer thickness[...]
Dariusz Siemiaszko, Iwona Nowakowska, Zenon Komorek
The influence of heating rate during sintering on mechanical properties of Fe40Al sinters at room temperature
DOI 10.15199/28.2016.5.11
Abstract
The results of a uniaxial compression test of Fe40Al (at. %) sintered powders are presented. Compression yield stress Rc0.2, ultimate strength Rcm, permanent deformation, and true compression strength at the maximum force point were determined. All Fe40Al sinters behaved like a plastic material; they were not brittle, and the sample after the compression test did not fall apart and was barrel-shaped. Observations of the microstructure revealed plastically-deformed grains. The obtained sinters were characterized by very high ultimate compressive strength (ok. 2700÷2800 MPa) and low yield stress (Rc0.2 approx. 280 MPa). This paper presents also XRD analyses, microstructure, and density of Fe40Al sinters. Key words: intermetallic alloys, iron aluminides, reaction synthesis, compression test, plasticity.1. INTRODUCTION Despite its obvious advantages, such as low density, good corrosion and oxidation resistance, and high strength at both room and elevated temperature [1÷3], the FeAl-based alloys are still only potentially used as replacements for expensive alloy steels; this is primarily due to their ductility and inherently low toughness, especially at ambient temperature [4]. It is generally known that the mechanical properties of iron aluminides are very sensitive to many factors, including aluminium content, order, heat treatment, the test temperature, alloying additions, environment, microstructure, and defects [5]. Due to the fragility of Fe-Al alloys, which increases with increasing aluminium content, alloys with an aluminium content of 40% are the most frequently analysed. FeAl alloys of 40% Al are characterized by high strength properties at an acceptable ductility. Due to the potential embrittlement of sintered FeAl powders, it is tested mostly by the compression test. Literature sources indicate that the yield stress of Fe40Al at ambient temperature ranges from 380 to 820 MPa [4, 6÷9]. The strain obtained during testing strength[...]
Monika Ewa Ostapiuk
Failure analysis of poly(phenylene sulphide)/short glass fibre composite in bending strength test
DOI 10.15199/28.2016.5.12
Abstract
Nowadays polymer composites are one of the most popular materials in the field of science and applying engineering. They combine various advantages, which are easy to manufacture, cost effectiveness and excellent performance. The great importance is choosing of an appropriate matrix for special composites elements working in different conditions. Very interesting technical material seems to be the thermoplastic resin poly (phenylene sulphide) (PPS) which can be used in automobiles, aircrafts and electro-/electronics technologies. Conventional thermoset composites have in recent years successfully found engineering applications but in contrast to PPS they have been limited for applying at higher temperature and difficulties in recycling. Regarding the lack of knowledge in terms of precise understanding on the failure basis, there has been not many publications on the degradation mechanisms of PPS with short glass fibres. In this article, the PPS/fibre fillers (containing 30% and 40% short glass fibers) has been introduced. It has been showed and discussed the phenomena and structure characterization after three point bending tests. It was carried out the macro- and microstructural observation. The plots of stress vs displacement indicate to brittle materials behaviour. All samples of the PPS 30% and PPS 40% composites subjected to 3-points bending test were destroyed in in the centre of the sample. It was confirmed that in short fibre composites, generally, the failure process is dictated by fibre/matrix separation which usually starts near the fibre ends. The scheme of cracking is similar regardless of fibre content. The bending stresses were higher in the composite with higher volume fraction of fibres. Key words: short glass fibers, thermoplastic resin, PPS, bending test.1. INTRODUCTION Nowadays polymer composites occupy a market share as one of the most popular applying engineering materials. They provide a combination of various advantag[...]
INŻYNIERIA MATERIAŁOWA 4/2016
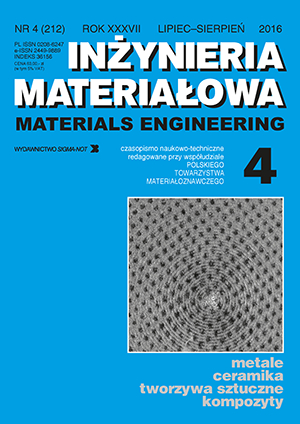
Beata Dubiel, Paulina Indyka, Adam Kruk, Izabela Kalemba-Rec, Tomasz Moskalewicz, Katarzyna Berent, Marta Gajewska
Characterisation of TCP phases in CMSX-4 single crystal superalloy subjected to high temperature annealing and creep deformation
DOI 10.15199/28.2016.4.1
Abstract
A high temperature exposure of nickel-base single crystal superalloys leads to a formation of topologically close packed (TCP) phases, what can deteriorate their creep strength. Therefore, the aim of the present work was to investigate TCP phases precipitated in CMSX-4 superalloy after a two-step treatment consisting of annealing at temperature of 1100°C followed by a creep deformation at temperature of 900°C. The microstructure of CMSX-4 superalloy exposed to a high temperature was investigated by means of scanning and transmission electron microscopy as well as scanning-transmission electron microscopy in high angle annular dark field mode. The chemical composition in nanoareas was determined using the high spatial resolution and high count rate energy dispersive X-ray spectroscopy. A three-dimensional characterization of the microstructure of annealed and creep tested single crystal superalloy was carried out by means of electron tomography. Results of microstructural investigation have shown that after the application of two-step high temperature exposure the TCP precipitates present in CMSX-4 superalloy are P and μ phases. The most pronounced differences in the chemical composition of the investigated P and μ phase particles are concerned with W and Re content. It was determined that the P phase contains a higher amount of W, while the μ phase is mostly rich in Re. Key words: single crystal nickel-base superalloys, annealing, creep, TCP phases.1. INTRODUCTION Single crystal nickel-base superalloys are especially designed for gas turbine blade and vane applications. The microstructure of single crystal superalloys consists of two phases, namely the γ phase matrix and cuboidal γʹ phase precipitates. To increase the high temperature creep resistance of single crystal superalloys, high amounts of refractory elements such as Mo, W and Re are added. These elements provide a solid solution strengthening, but unfo[...]
Krzysztof Czyż, Jan Marczak, Roman Major, Aldona Mzyk, Antoni Rycyk, Antoni Sarzyński, Marek Strzelec, Przemysław Wachulak
The influence of surface topography elaborated by prism optics based laser interference modification on cell differentiation
DOI 10.15199/28.2016.4.2
Abstract
The direct laser interference lithography, based on bi-prism, tetragonal pyramid and an axicon was used as a tool for periodical structuring of different bioscaffolds. The simple, source laser system with stable Nd:YAG laser resonator, amplifying system (energy up to 1 J) and prism-based interferometer optics gave possibility to create periodical, linear, dotted and even circular surface structures, with high degree of periods, width and depth control. The general idea consists of the imitation of the structure and function of tissues and adoption of these solutions for the material science. It is well known that the influence of the artificial material on the cellular processes related to the differentiation, proliferation and growth are dependent on the chemical composition and surface topography as well as mechanical properties of applied materials. The most recent studies focus on the cell interaction with flat scaffolds. However, cells are found covering a highly rough surface in the blood vessels. The work was related to reconstruction of the structure and function and topography of luminal side of the blood vessels. The most important aspect was to recreate cellular niches which plays specific function on the activation and differentiation of stem cells. The mechanical stresses generated at any certain site depend on the surface micropatterns of the material as well as the other signals that cell receives from chemical stimuli. This work is one of the first attempts to determine correlation of surface micro-topography with biochemical stimulation by adsorbed on the materials surface molecules and both factors potential influence on cellular response. The study was aimed at showing the mechanism of human endothelial progenitor cells adhesion, morphology and function control in response to surface patterning. It was found that micro-channels enhanced intercellular connections forming tight junctions and the appropriate progenitor cell diff[...]
Małgorzata Norek
Porous anodic alumina formed on AA6063 aluminum alloy in a two-step process combining hard and mild anodization
DOI 10.15199/28.2016.4.3
Abstract
Two-step process combining hard (in 0.3 M oxalic acid solution) and mild (in 0.1 M phosphoric acid solution) anodization at voltages ranging between 120 and 180 V was applied to prepare porous anodic alumina (PAA) on AA6063 alloy foil. The influence of ethanol on geometrical parameters of the PAAs was also tested. The analysis of the geometrical parameters as well as the current/voltage vs time transients suggested that alloying elements present in the AA6063 alloys play an important role in the relaxation of mechanical stresses at the metal/oxide interface occurring during the PAA’s growth. The effect contributed to comparable interpore distance Dc values (between 270÷370 nm) and similar regularity ratio parameter (RR) in the samples anodized in ethanol-free and ethanol-modified electrolyte, despite much larger average current densities registered for the former samples. The hexagonal pore ordering increased with the applied anodizing voltage. Key words: hard anodization, guided anodization, porous anodic alumina (PAA).1. INTRODUCTION Highly-ordered porous anodic alumina (PAA) is one of the most attractive templates for nanofabrication [1, 2]. Its geometrical parameters including pore diameter and pore arrangement, interpore distance, or PAA film thickness are easily controlled by anodizing conditions such as type of electrolyte, applied voltage, anodization time, or bath temperature [3, 4]. Usually PAA is fabricated on high-purity aluminium (99.999%) which by far hoists its production costs. Therefore, from economical point of view a replacement of the expensive high-purity aluminium for low-purity aluminium which is about two orders of magnitude cheaper is very desirable. The structural and compositional features of aluminium substrate play an important role in formation of long-range ordered porous anodic alumina. The low-purity aluminium contains a variety of alloying elements, which can bring about new behaviors during ano[...]
Piotr Panek, Robert Piotr Socha, Mari Juel, Paweł Zięba
The liquid phosphorus source for Si solar cells fabrication
DOI 10.15199/28.2016.4.4
Abstract
A new liquid source of phosphorus atoms (SPA), dedicated to emitter formation in Si solar cells, was elaborated on the basis of H3PO4. The important properties of this solution, that can be deposited by the spray method, make possible the formation of easily removable phosphosilicate glass (PSG) when the diffusion process is performed. The PSG formed from SPA and from conventional POCl3 source were investigated by X-ray photoelectron spectroscopy. The diffusion depth profiles were determined by a secondary ion mass spectrometry. The presented solution and technology of the n-type diffused layer formation allowed for precise shaping of the phosphorus doping profile. Relatively short diffusion process, which lasted only for 3 minutes, resulted in the sheet resistance between 30÷120 Ω/□, that is appropriate for the solar cells applications. The solar cells with the use of new donor source were produced and characterized by the current-voltage and spectral response techniques. The simple technology of the emitter fabrication from the liquid solution deposited by a spray method is expected to become more cost-competitive in major PV companies than the traditional POCl3 based technique. Key words: phosphorus diffusion, silicon solar cell.1. INTRODUCTION The market requirement for the crystalline Si (c-Si) solar cells production forces the cost reduction per unit power. This task can be achieved either by further enhancing the energy conversion efficiency or by lowering the fabrication costs that requires the development of new production methods. The crucial step in the manufacturing of the crystalline silicon solar cells is the emitter formation. The emitters can be formed using several techniques such as thermal method, spin-on, spray, screen-printing, chemical vapour deposition, epitaxy, evaporation, implantation or closed contact. There are two compounds industrially applied for phosphorus doping i.e. POCl3 liquid source and H3P[...]
Damian Batory, Anna Jędrzejczak, Anna Sobczyk-Guzenda, Witold Szymański, Piotr Niedzielski
Studies of thermal stability of a-C:H:Si coatings produced by radio-frequency plasma assisted chemical vapour deposition (RF-PACVD) method
DOI 10.15199/28.2016.4.5
Abstract
In this work the thermal stability of silicon-doped diamond-like carbon (DLC) films was investigated. The studied coatings were produced by radio-frequency plasma assisted chemical vapour deposition (RF-PACVD) method with use of tetramethylsilane (TMS) as a silicon precursor. As-deposited Si-DLC coatings with three different silicon concentrations were annealed at 400°C, 500°C, and 600°C for 1 hour in air atmosphere. For comparison DLC coatings were also examined. It has been shown that the level of disorder of Si-DLC increases with the increase of silicon concentration. Silicon admixture improves the thermal stability of Si-DLC coatings by slowing down and delaying the graphitization processes compared to the undoped DLC films. Furthermore, an increase in hardness of the Si-DLC coatings annealed at the temperature of 400°C has been observed. The DLC and Si-DLC coatings with the lowest Si concentration annealed at 500°C, and all of the coatings annealed at 600°C have been completely degraded. The coatings with the highest concentration of silicon that have stood the annealing process at 500°C have demonstrated a high degree of graphitization and degradation, manifesting itself in the lowest mechanical properties and a significant reduction in their thickness. Key words: thermal stability, silicon doping, DLC films.1. INTRODUCTION Diamond-like carbon (DLC) films are characterized by many unique properties. These include high biocompatibility [1], high hardness [2], low coefficient of friction, [3, 4] good anti-wear [4] and anti-corrosion [5] characteristics. Hence, these films are commonly used as protective coatings in automotive industry, magnetic data storage, machining tools and biomedical applications [1÷3, 6]. However, DLC coatings have several known disadvantages. One of them, severely limiting their large scale application possibilities is the low thermal stability at high working temperature. It has been reported that DLC coating[...]
Tomasz Ratajski, Izabela Kalemba-Rec, Beata Dubiel
Influence of polyethylenimine on the electrophoretic deposition of SiO2 and Ni/SiO2 coatings on 316L stainless steel
DOI 10.15199/28.2016.4.6
Abstract
The aim of the present work was to investigate the influence of polyethylenimine, a cationic polymer surfactant, on the microstructure and corrosion resistance of SiO2 and Ni/SiO2 coatings electrophoretically deposited on 316L stainless steel. The relationship between zeta potential and pH of the ethanol-based suspensions of SiO2 and Ni powder particles with addition of polyethylenimine was determined. The parameters of electrophoretic deposition process (applied voltage, time, distance between electrodes) were developed to prepare good quality coatings. Cathodophoresis from suspensions with polyethylenimine addition was performed with slightly lower applied voltage and time as compared to anodic deposition of coatings without surfactant. The microstructure of the coatings, their surface roughness and adhesion to the substrate were investigated. The protective behaviour of the coatings was studied by potentiodynamic measurements in 3.5% NaCl water solution. The microstructure and properties of the coatings were compared with those obtained without polyethylenimine addition. It was determined that the microstructure of SiO2 and Ni/SiO2 coatings deposited from suspensions containing polyethylenimine was more uniform and contained smaller amount of cracks and voids than the coatings achieved without polyelectrolyte. It was also observed that the quality improvement of the coatings deposited on 316L steel due to addition of polyelectrolyte with binding properties leads to increase of their corrosion resistance. Key words: electrophoretic deposition (EPD), SiO2 coatings, Ni/SiO2 composite coatings, polyelectrolyte, polyethylenimine.1. INTRODUCTION 316L stainless steel is widely used in applications involving severe corrosive conditions. Due to the formation of a thin chromium oxide film the steel exhibits good corrosion resistance in oxidising media [1]. However, in Cl- containing environment, deterioration of the passive film occurs and the stee[...]
Monika Solecka, Agnieszka Radziszewska, Agnieszka Kopia, Magdalena Rozmus-Górnikowska, Jan Kusiński
Investigation of Ni-base coatings after corrosion test
DOI 10.15199/28.2016.4.7
Abstract
Inconel 625 and 686 are Ni-Cr-Mo alloys used for its high strength, outstanding corrosion resistance, and excellent fabricability. For this reason, these alloys are typically used as a one of the most important coating material and can be applied to chemical and petrochemical plants, power generation sector, heat exchanger tubing for boilers of waste incinerators. To perform the Ni-base weld overlays, without introducing too much Fe, a new weld technique called Cold Metal Transfer (CMT) was used. This paper presents the mechanisms of high-temperature corrosion, microstructure and chemical composition of boiler elements after the waste incineration form ashes at 650°C from 500 h. Microstructure examinations of the Inconel 625 and Inconel 686 corroded surface were carried out by scanning electron microscopy (SEM) supported by energy dispersive spectroscopy (EDS). The phase compositions of the corroded surfaces were carried out by means of X-ray diffraction. Key words: Inconel 625, Inconel 686, corrosion layer.1. INTRODUCTION Corrosion-resistant Ni-base superalloys like Inconel 625 and Inconel 686 are widely used in several industrial sectors, including petrochemical or power generations, due to their high performance in aggressive environments. The field of their application as the structural materials depends, to a large extent, on the concentrations and the ratios between the contents of their main alloying components, primarily, chromium and molybdenum. Nowadays, Ni-base alloys are typically used to manufacture engineering components, or coatings for protection of cheaper metallic substrates, which should work in extreme conditions including mechanical loads and an aggressive environment at high temperature. Due to the excellent high temperature corrosion resistance and good strength at high temperatures Ni-base alloys can work in aggressive environments [1, 2]. Inconel 625 is a metallic materials, austenitic alloy, showing an extrao[...]
Waldemar Ziaja, Maciej Motyka, Jan Sieniawski
Microstructural factors in the primary creep stage of two-phase titanium alloy
DOI 10.15199/28.2016.4.8
Abstract
One of the major areas of titanium alloys application includes discs and blades of compressors in turbine engines. In titanium alloys, significant strain can accumulate as a function of time, at stresses well below the yield strength at the homologous temperature below 0.25, even at room temperature. Life prediction for elements made of titanium alloys which is based solely on steady state creep parameters is in some cases not adequate due to large primary creep strains. In the case of rotating components of aero-engines small dimensional tolerances can be threatened and transient creep strains must be taken into account in modelling of overall creep deformation. Creep and fatigue properties of two-phase titanium alloys show strong dependence on microstructure, especially morphology of the α and β phases which can be controlled to certain extent by proper selection of hot working and heat treatment conditions. In the paper the primary creep behaviour of Ti-6Al-2Mo-2Cr alloy (VT3-1) at elevated temperature was investigated. The microstructure of the alloy was varied by means of changing conditions of heat-treatment. Creep tests were carried out on the alloy with globular and lamellar microstructure at the temperature of 450°C. Primary stage of the creep process was described using various constitutive laws. Applicability of power-law and logarithmic equations for describing strain evolution was verified. The influence of the initial microstructure on the primary creep strain and strain rate at the onset of steady-state creep stage was analysed. Key words: two-phase titanium alloys, primary creep, microstructure.1. INTRODUCTION Over the recent decades titanium alloys became a prime material choice for designers of heavily loaded engineering components operating in demanding environments. Favourable combination of properties like high specific strength at room and intermediate temperature range, good fracture toughness and corrosion [...]
Mateusz Kopeć, Paweł Grzywna, Dominik Kukla, Zbigniew Kowalewski
Evaluation of the fatigue damage development using ESPI method
DOI 10.15199/28.2016.4.9
Abstract
Fatigue damage process developing in structural materials under long-term cyclic loading is still an unsolved problem of modern engineering. Attempts to assess a degree of materials degradation under fatigue conditions on the basis of changes in the areas of local strain concentration determined by optical methods can be treated as the promising contemporary research direction of majority of scientific centres in the world. In most cases, fatigue damage has a local character and it is based on damage development leading to generation of cracks appearing around structural defects or geometrical notches. An identification of these areas and their subsequent monitoring requires a full-field displacement measurements performed on the objects surfaces. It seems that modern contemporary optical methods for displacement components measuring on the surfaces of structural elements or tested specimens are suitable for such purpose. Digital Image Correlation (DIC) and Electronic Speckle Pattern Interferometry (ESPI) are nowadays the most widely used testing methods in this area. Both of them enable capturing of displacement and strain components distributions. This paper presents an attempt to use the ESPI method for fatigue damage evaluation and its monitoring on specimens made of the aluminide coated nickel super-alloys. Flat specimens were subjected to cyclic loading. The fatigue tests were interrupted several times in order to perform a static loading during which the optical measurements were carried out. An analysis of the results captured by the ESPI system allowed indication of places of the greatest stress concentration and demonstration of the damage development process as a function of the increasing number of cycles. Key words: fatigue, damage, super-alloy, Electronic Speckle Pattern Interferometry.1. INTRODUCTION Experimental assessment of damage development in materials subjected to cyclic loading requires continuous monitoring of the disp[...]
INŻYNIERIA MATERIAŁOWA 3/2016
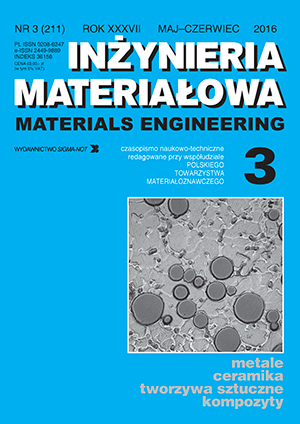
Aleksandra Towarek, Joanna Zdunek, Jarosław Mizera, Anna Dobkowska, Rafał Molak
Influence of the corrosive environment on the Portevin-Le Chatelier plastic instability phenomenon in Al-1Mg and Al-3Mg model alloys
DOI 10.15199/28.2016.3.1
Abstract
The aim of this work was to indicate the influence of changes on the surface of materials caused by the corrosive medium (3.5% NaCl solution) on the intensity and character of the Portevin-Le Chatelier effect in model aluminium alloys. For this purpose, two Al alloys, containing 1% and 3% of magnesium, were subjected to tensile testing in the as-cast state and after the exposition in NaCl solution for various time. Several electrochemical measurements were held to determine materials’ corrosive behaviour and microscopic observations to evaluate the surface character of the samples. High corrosion resistance of the materials resulted in a very slight alteration of their surface development, which didn’t lead into any significant variations in the plastic instability phenomenon PLC. Key words: Portevin-Le Chatelier effect, aluminium alloys, plastic instability, corrosion. 1. INTRODUCTION Portevin-Le Chatelier effect (PLC effect) is a well-known phenomenon occurring in many aluminium alloys during deformation [1], manifesting itself in a form of characteristic serrations on the stress-strain curve, caused by rapid changes of force in small extensions. It can lead to inhomogeneous deformations in materials microstructure, resulting in the deterioration of its mechanical properties [2]. Apart from the most commonly analysed structural factors, like grain size, precipitations or texture, there are some extrinsic ones which can also strongly influence materials vulnerability to PLC effect [3]. Abduluyahed in his research [4, 5] compared serrated flow in 316 and 316L austenitic steels during tensile testing in air and in vacuum. He reported a considerable decrease in serration frequency in vacuum conditions, which can be subjected to the fact that there is no oxygen layer on the surface, which could crack during deformation and work as a stress concentration. Temperature was considered as a factor influencing PLC effect, by Yilm[...]
Grażyna Mrówka-Nowotnik, Jan Sieniawski, Andrzej Nowotnik, Andrzej Gradzik
Analysis of precipitation strengthening process in 2xxx aluminium alloys
DOI 10.15199/28.2016.3.2
Abstract
This paper is showing the results of study devoted to determination of the chemical composition and strengthening process parameters effect on the precipitation sequence of intermetallic phases in the supersaturated 2xxx aluminium alloys. This study was based on a calorimetric study where temperature’s effects were determined when precipitation process occurred during heating with different heating rate of the supersaturated alloys group of 2xxx. Based on the calorimetric curves and estimated values of ln(Q/T2) and 1000/RT an activation energy for precipitation and dissolution of phase components were evaluated. Key words: aluminium alloys, precipitation strengthening, calorimetry, activation energy. Inżynieria Materiałowa 3 (211) (2016) 104÷108 DOI 10.15199/28.2016.3.2 © Copyright SIGMA-NOT MATERIALS ENGINEERING 1. INTRODUCTION The 2xxx series of aluminium alloys generally contain 2 up to 10% copper, with smaller additions of other elements. The copper provides substantial increases in strength and facilitates precipitation hardening. The introduction of copper to aluminum can also reduce ductility and corrosion resistance [1, 2]. Thus, the most common applications for these type of alloys are aerospace and automotive industries. Due to both the development of new alloys, as well as the constantly increasing demands on their performance, there was a still need to examine the effect of chemical composition, kinetic of precipitation processes from supersaturated solutions and the influence of strengthening phases on the final mechanical properties of newly developed aluminium alloys. The mechanism of age hardening responsible for strengthening is based on the formation of intermetallic products through the decomposition of a metastable supersaturated solid solution SSS obtained by solution treatment and quenching. Since the interactions between the decomposition products and the dislocations are mainly responsible for the[...]
Przemysław Litwa, Krzysztof Perkowski, Izabela Kobus, Marta Ziemnicka-Sylwester, Tomasz Czujko, Robert A. Varin
The effect of porosity on thermal properties of TiB2-based Cu cermets obtained by ball milling and containerless HIP
DOI 10.15199/28.2016.3.3
Abstract
he effect of porosity on microstructure and thermal properties of titanium diboride (TiB2) based cermets with Cu binder was investigated. It has been demonstrated a good wettability of the TiB2-Cu interfaces which allows for heat flow through it easily but formed microporosity (25÷32 %) and related structural defects in the sintered cermets affects the thermal conductivity. The specific heat changes exponentially with temperature and amounts to 0.37 J∙g-1K-1 at 298 K for the TiB2-Cu (20 vol. %) cermet with the lowest porosity. The X-ray diffraction (XRD) analysis confirmed that TiB2-Cu is the stable system and there was no reaction between TiB2 and Cu. The dependence of microstructure and composition on thermal properties of sintered the TiB2-Cu cermet alloys was discussed. Key words: titanium diboride, TiB2-Cu cermets, ceramic matrix composites (CMCs), hot isostatic pressing, HIP, thermal properties. Inżynieria Materiałowa 3 (211) (2016) 109÷114 DOI 10.15199/28.2016.3.3 1. INTRODUCTION Titanium diboride (TiB2) is one of a few refractory metal borides with an attractive combination of properties such as high melting point (3225°C), ultra-high hardness (25 GPa), high strength to density ratio, good thermal and electrical conductivity (96 W∙m-1K-1 and 22∙106 Wcm, respectively) and wear resistance [1, 2]. TiB2 can be used to produce dense constructive sintered materials for high-temperature structural applications as well as for control rod elements with a high-thermal neutron absorption in nuclear reactors. However, it is well known, that wide applications of TiB2 ceramic are limited due to poor sintering ability, which requires extremely high temperature [3, 4]. The interesting approach for obtaining the TiB2 based cermets is the sintering method by hot isostatic pressing (HIP). In this way by intensive mass transfer the sintering process is carried out in shorter time and at lower temperature. The lower temperatu[...]
Katarzyna Natalia Braszczyńska-Malik, Elżbieta Przełożyńska
Fabrication of AM50 magnesium matrix composite with titanium particles by stir casting method
DOI 10.15199/28.2016.3.4
Abstract
The paper focuses on the experimental magnesium matrix composite reinforced with Ti particles fabricated by the stir casting method. The main objective of the study was to develop a new type of composites with metallic particles fabricated by a simple and inexpensive casting method. For this purpose, one of the cheapest and most widely used alloys, AM50 (Mg-Al-Mn system), was selected as the matrix alloy. The investigated material was prepared on the basis of the AM50 commercial magnesium alloy with 30 wt % spherical Ti particles. The experimental composite was obtained by introducing Ti particles to the mechanical mixing of the molten magnesium alloy under a protective atmosphere. The prepared composite suspension was gravity cast into a metal mould. Analyses of the AM50-Tip composite microstructure were carried out by light microscopy, scanning electron microscopy (SEM + EDS) and X-ray diffraction (XRD). Brinell hardness of the examined material was also measured. Additionally, the weight fraction of the Ti particles was verified by determining their volume fraction using the linear method. The obtained composite exhibited uniform distribution of the Ti particles within the magnesium matrix alloy. According to the presented results of the investigation, no new phases were revealed by the microstructure observations and XRD techniques. The phase composition of the composite was typical for the used component. The matrix alloy was composed of an α-Mg, α + γ eutectic and Al8Mn5 intermetallic phase. Key words: magnesium matrix composites, Ti particles, stir casting, microstructure. Inżynieria Materiałowa 3 (211) (2016) 115÷119 DOI 10.15199/28.2016.3.4 1. INTRODUCTION Metal matrix composites (MMCs) reinforced with different fibers or particles are among various composites of the most recent structural construction materials. Obtaining the designed properties of these composite materials depends, however, on achieving the des[...]
Adam Gnatowski, Mateusz Chyra
Examinations of thermomechanical properties and structure of polyethylene with cardboard fibre and colourant composites after electrochemical ageing
DOI 10.15199/28.2016.3.5
Abstract
The use of fillers in the production of plastic products is intended to improve their properties, the wider use and reduce prices. The ageing of polymers results in deterioration of strength properties of the material. Forecasting changes caused due to ageing allows to determine the feasibility of application of the composites under certain conditions. The article presents the results of investigations of polyethylene (Hostalen 7260, Lyondellbasell) with cardboard and dye composites before and after electrochemical ageing. Ageing process was performed in special chamber, in water solution of NaCl (35‰) at pH 7 and at 20°C for 720 h (current 0.3 A). Samples with the addition of 2% dye, 2% dye and 2% cardboard, 2% dye and 4% cardboard, 2% dye and 6% cardboard were tested. The carboard filler was made by mechanical fragmentation. The samples were injected using a KraussMaffei KM65-160C1 injection moulding machine. Tensile strength was measured. The thermal properties were analysed using a DSC method. Structure was observed using light microscope. Hardness was determined with ball pressing method. The aim of the investigations was to determine the influence of the filler on the composite properties and to receive a new, cheaper material. Changes in the degree of crystallinity, the melting point range, structure of the tested materials were revealed. The changes in mechanical properties of polyethylene with filler and dye before and after ageing were observed. The studies show that the electrochemical ageing causes significant changes in the properties of the tested materials Key words: polyethylene, composites, dye, cardboard, structure, thermomechanical properties. Inżynieria Materiałowa 3 (211) (2016) 120÷125 DOI 10.15199/28.2016.3.5 © Copyright SIGMA-NOT MATERIALS ENGINEERING 1. INTRODUCTION Polymeric composites are manufactured using the three methods: physical, chemical and physical-chemical. The physical method is the most po[...]
Zbigniew Oksiuta
Study of microstructure and mechanical properties of 14% Cr ODS steel produced by hot isostatic pressing followed by hot forging
DOI 10.15199/28.2016.3.6
Abstract
Consolidation by hot isostatic pressing followed by hot forging of a mechanically alloyed ODS Fe-14% Cr-2% W-0.3% Ti-0.3% Y2O3 (in wt %) ferritic steel powder was applied to find the effect of those methods on the microstructure and mechanical properties of the alloy. Microstructure investigations of the ODS steel revealed that after hot isostatic pressing bimodal-like microstructure with fine and coarse grains up to a few microns was observed. Hot forging process, performed at about 900°C with 50% of deformation, did not improved microstructure homogeneity and grains elongated towards radial direction were observed. High temperature tensile tests revealed that hot forging improves the tensile strength of the as-HIPped ODS steel. However, the ductility and upper shelf energy decreased. This can be related to the microstructure of the ODS steel observed for both consolidation methods and emphasises a necessity of further optimization of hot forging parameters. Key words: ODS ferritic steel, hot isostatic pressing, hot forging, tensile testing, Charpy impact properties. Inżynieria Materiałowa 3 (211) (2016) 126÷130 DOI 10.15199/28.2016.3.6 © Copyright SIGMA-NOT MATERIALS ENGINEERING 1. INTRODUCTION An oxide dispersion strengthened (ODS) reduced activation ferritic (RAF) steel is an advanced superalloy considered to be used as the most promising candidate material for structural components in the future fusion reactor. The ODS reduced activation ferritic steel can be obtained through selection of the appropriate alloying elements with a low activation ratio. Therefore, such widely alloying elements used in steels production as Al, Ni, Mo, Cu, Nb and N have to be eliminated and replaced by low activation elements, e.g. Fe, Cr, W, V, Ti, Si and C. These elements also ensure fully ferritic (BCC) structure. In addition, in the ODS RAF steel harmful elements like Ag, Ho, Bi, Co, Sm, Lu, Dy, Gd, and Cd must be restricted to a very low le[...]
Marcin Godzierz, Paweł Wilkołek, Gözden Torun, Tomasz Pawlik, Małgorzata Sopicka-Lizer
Influence of leather tanning waste addition and sintering parameters on physical and mechanical properties of ceramic granules
DOI 10.15199/28.2016.3.7
Abstract
This paper presents results of manufacturing the ceramic porous granules made of the local waste materials. These granules were produced from the mixture of the car wind-shield glass contaminated by residuals of the PVB foil and aluminosilicate-based mine slates. Addition of the leather tanning wastes was used in order to increase granules porosity without significant decrease of mechanical properties. The paper shows the effect of tanning wastes addition and sintering parameters on the properties of the resultant granules in comparison to the leather-free product. Porosity, apparent density and water absorption were examined according to EN 1097 standard, and compressive strength was examined according to UNE-EN 13055-1 standard. Differences in the microstructure of granules were examined using scanning electron microscope. Partial substitution of both starting materials by tanning wastes and/or the two-step sintering regime could significantly improve the physical properties, what has been shown in the present paper. Key words: ceramic granules, leather tanning waste, recycling, waste management, windshield glass. Inżynieria Materiałowa 3 (211) (2016) 131÷136 DOI 10.15199/28.2016.3.7 © Copyright SIGMA-NOT MATERIALS ENGINEERING 1. INTRODUCTION Nowadays, there are several issues related to recycling the car windshield glass. One of these problem is related to the layered structure of a car windshield. Two layers of glass are separated by a polymer layer of polyvinyl butyral (mainly known as PVB), which improves mechanical properties of the laminated material but simultaneously it prevents the separation of layers in the waste glass during a mechanical treatment. Advanced technology allows to separate those layers during screening resulting in separation of PVB as a large-sized fraction from the fine glass powder. It is impossible to produce the windshields again from these materials, but the PVB scraps can be used once more as an[...]
Maria Richert, Wacław Muzykiewicz, Katarzyna Łyp-Wrońska
Profile and professional career of graduates in Materials Engineering, AGH Faculty of Non-Ferrous Metals
DOI 10.15199/28.2016.3.8
Abstract
The Faculty of Non-Ferrous Metals at the AGH University of Science and Technology in Krakow offers, among others, studies of materials engineering focused on non-ferrous metals. The Faculty has already educated 4717 specialists, including 4280 graduates educated in full-time programmes, mainly with the degree of master of science, engineer. Throughout the whole time of its activity, the Faculty has promoted 264 doctors of technical sciences and 55 associate professors. Education in Materials Engineering at the Faculty of Non-Ferrous Metals is carried out at three levels of learning and includes knowledge, skills and social competence, all of them being a response to the needs of modern industry. Classes are run by the renowned teaching staff and researchers. Students can develop their interests and learn new skills by participation in the activities of Student Science Circles. Graduates in Materials Engineering are specialists deeply involved in the problems of the design, manufacture, application, bonding and testing of materials (mainly metallic) to support the need for knowledge development in the field of technology and processing of steel, special alloys, metallic sinters and composites, as well as surface engineering, welding and quality. It seems that, considering the present economic climate, these are aptly chosen fields of study providing work in the non-ferrous metals industry and related industries, and educating creative individuals, successfully coping with the difficult job market. Graduates in Materials Engineering are well prepared to work as experts in shaping the structure and technological properties of metallic materials by methods of thermomechanical and physicochemical treatment. They are qualified to conduct research on the modelling of new materials and advanced technologies. The graduates have no major problems with finding jobs and are employed mainly in all those areas where in-depth knowledge of the structure and de[...]
INŻYNIERIA MATERIAŁOWA 2/2016
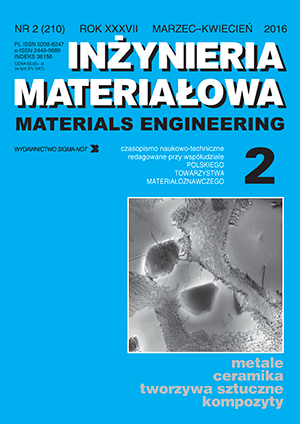
Agnieszka Szczotok, Barbara Kościelniak
Characterization of IN713C superalloy microstructure after high temperature creep test by LM, SEM and STEM
DOI 10.15199/28.2016.2.1
Abstract
This work focuses on the influence of creep phenomenon on the cast IN713C nickel-based superalloy. The carrot-shape IN713C superalloy castings were produced in an investment casting cluster mould and the creep test samples were then prepared from the castings. The creep tests were carried out in order to investigate processing-microstructure-property relationships. The resultant macro- and microstructures were observed and characterized after the creep tests using light microscopy, scanning electron microscopy and scanning transmission electron microscopy. The aim of the analysis was to reveal the changes in the microstructure that occurred as a result of the creep and to identify the phases that participate in voids formation, and crack generation and propagation during the creep tests. It was confirmed that the creep resistance of the IN713C superalloy is negatively affected by some structural characteristics such as porosity, (γ + γ′) eutectic or carbide precipitates along the grain boundaries. Our work confirms that a combination of thermal conditions with a tensile force affected the microstructure of IN713C nickel-based superalloy causing changes in morphologies of the existing precipitations and phase transformations, as in the case of the carbides. Additionally, carbide sulphides containing primarily Zr and intermetallic phase including mainly Ni and Zr were observed. Key words: IN713C, superalloy, creep, microstructure.1. INTRODUCTION Creep, fatigue and the interaction between them play important roles in determining the lifetime of many device components used at elevated temperature. Turbine blades made of nickel-based superalloys are subjected to complex thermal and mechanical creep and fatigue loads [1, 2], resulting in a marked change in microstructure during creep as the originally cubic morphology of the γ′ precipitates becomes directionally coarsened (raft-like) perpendicular to the direction of t[...]
Stanisław Roskosz, Rafał Cygan
Investment casting parameters impact on IN 713C nickel-based superalloy microstructure
DOI 10.15199/28.2016.2.2
Abstract
The basic process for manufacturing of aircraft engine hot section elements made of nickel-based superalloys is investment casting using multilayer ceramic shell moulds. Introduction of new engines designs with higher thrust, lower fuel consumption and lower noise emissions enforce continual modification of casting materials, models, ceramic moulds, including melting, pouring and heat treatment processes parameters. The aim of this study was to determine the effect of pouring temperature and cobalt aluminate modifier in the subsurface layer of the mould on macrostructure of the IN 713C castings. The size of misruns, chill, columnar and equiaxed zones on the surface of the wedge castings is most affected by pouring temperature. Additionally it was proved that cobalt aluminate is an effective modifier of the IN713C superalloy causing not only refinement of equiaxed grains, but also reduction in the columnar grain size fraction. Key words: investment casting, superalloys, microstructure, grain size, dendrite arm spacing.1. INTRODUCTION IN 713C superalloy in as-cast state is mainly used, among others, for aircraft engine components. These elements are casted using the lost-wax method with multilayer ceramic moulds. Casted gas turbine blades are characterised by coarse grains of heterogeneous microstructure. The casting often does not meet mechanical properties required from the kinds of elements used in the aerospace industry [1, 2]. The microstructure improvement of nickel-based superalloy blades may be obtained by appropriate shaping of grains size during the casting process [3, 4]. Controlled grain size can be achieved by specific pouring temperature, mould temperature, and the use of modifier in the surface layer of the mould [5, 6]. Highest grain refinement of nickel-based superalloys was obtained with application of cobalt aluminate modifier [7, 8]. The aim of presented study was to determine the effect of pouring temperature and Co[...]
Aneta Szewczyk-Nykiel, Jan Kazior
The influence of aging temperature on corrosion resistance of sintered 17-4 PH stainless steel
DOI 10.15199/28.2016.2.3
Abstract
Among the precipitation hardening stainless steels, martensitic grade of 17-4 PH has a special importance. This steel exhibits a good combination of high mechanical properties and good corrosion resistance. Therefore it is widely used in many branches of industry. The pitting corrosion behaviour of sintered 17-4 PH steel processed under different aging processing conditions in 0.5 M NaCl solution at 25°C was studied by open circuit potential measurement and potentiodynamic polarization technique. Compared with the sintered 17-4 PH, the corrosion resistance of the solution treated and aged steels were improved, as evidenced by a noble shift in open circuit potential, a higher pitting potential, a higher polarization resistance and a lower passive current density. Considering the influence of aging temperature on the pitting behavior of the 17-4 PH steel, it can be concluded that steel aged at 480°C exhibited the highest corrosion resistance in 0.5 M NaCl solution. While aging treatment at 500°C resulted in the worst corrosion resistance. In addition, the hardness of the solution treated and aged 17-4 PH was higher than that of the sintered steel. Key words: 17-4 PH stainless steel, pitting corrosion, hardness.1. INTRODUCTION It is known that the corrosion destruction is one of the main sources of material loss. And furthermore it contributes to the pollution of the environment and even constitutes a risk to human health. The problem of materials durability in natural and artificial environments is extremely important from the viewpoint of design and also application of constructions, devices, tools and etc. The degradation of the materials and the environment as a result of corrosion can be effectively reduced by appropriate prevention, mainly by using methods of anticorrosive protection and adequate selection of materials. The steels containing at least 10.5 wt % chromium and other elements (such as nickel or molybdenum) are more resist[...]
Grzegorz Kwiatkowski, Dariusz Rozumek
Wpływ parametrów obróbki cieplnej na strukturę i rozwój pęknięć zmęczeniowych bimetalu stal-tytan
DOI 10.15199/28.2016.2.4
Abstract
1. CEL PRACY Celem pracy było zbadanie zmian strukturalnych oraz trwałości zmęczeniowej po cyklicznym zginaniu bimetalu stal-tytan poddanego uprzednio wygrzewaniu w różnej temperaturze. 2. MATERIAŁ I METODYKA BADAŃ Badaniom poddano próbki pobrane z blach wykonanych za pomocą metody zgrzewania wybuchowego przez Z.T.W EXPLOMET S.J., w których materiałem podstawowym była płyta stalowa SA-516 Gr. 60, natomiast materiałem nakładanym tytan SB-265 Gr. 1. Skład chemiczny materiałów przed połączeniem (z certyfikatu załączonego do materiału) przedstawiają tabele 1 i 2. W celu eliminacji naprężeń własnych powstałych w procesie zgrzewania wybuchowego plater został poddany wygrzewaniu w temperaturze 500°C, 600°C, 700°C, 800°C i 900°C z szybkością nagrzewania 90°C/h. Następnie materiały wygrzewano przez 2 h i chłodzono z piec[...]
Monika Krzywicka, Jerzy Grudziński, Jarosław Tatarczak, Piotr Ścibisz
Study on the surface of the polymer insert of the knee replacement using pulsed thermography
DOI 10.15199/28.2016.2.5
Abstract
Providing of joint prostheses with high reliability is particularly important because the loss of their functional properties may cause invasive surgery revision. The main exploitation problems with prostheses are loosening (septic or aseptic) and the wear of inserts made of UHMWPE. Identification of the types and mechanisms of cooperating surfaces wear of the knee prostheses affects the improvement of materials selection, design and increase their reliability and durability. Typical kinds of damage of UHMWPE element of the prosthesis include abrasive wear, plastic deformation and creep, fatigue wear (pitting), changing the chemical composition and colour, changing in the structure, cracking. This paper presents the test results of the UHMWPE insert surface of the knee replacement which was used by the patient for 13 months. Microscopic studies, pulse thermography and 3D scanning of the UHMWPE insert were carried out. 3D scanning element has paved the way for reconstruction of the shape of the working surface of the insert of prosthesis. Surface defects in the tested insert were revealed by using innovative methods of pulsed thermography. In order to identify defects, located on the surface, microscopic studies were carried out. They have shown a complex mechanism of wear. Many signs of abrasive wear, fatigue wear (pitting) and microcracks have been observed. Analysis of the bio-bearing operation also indicates the signs of early fatigue wear. The causes of wear of tested elements include too high load applied exceeding several times the weight of the human body, closed space in which products of friction are accumulated. Key words: knee replacement, wear mechanisms, ultra-high molecular weight polyethylene.1. INTRODUCTION The knee joint is the most often undergoing traumatic damage and is the most susceptible to the occurrence of various types of pathologies in the human body. A deformation of the joint is caused by a degenerative disease a[...]
Witold Sarna, Janusz Kozakiewicz, Jarosław Przybylski, Krystyna Sylwestrzak
RVC - reticulated vitreous carbon. Structure, precursor polymer materials, process of manufacturing and applications
DOI 10.15199/28.2016.2.6
Abstract
In this paper the review of literature data concerning preparation, properties and applications of Reticulated Vitreous Carbon (RVC) is presented. Vitreous carbon is a kind of carbon material with specific structure which deviates from crystalline structure of graphite as it has various defects of graphene layers (gaps, five-part rings, interstitial atoms or hetero-atoms substituted instead of carbon atoms) without mutual orientation and fixed distance between layers. Such structure is called “turbostratic" and it is characteristic for materials obtained through carbonization (pyrolysis) of organic substances, usually organic polymers. Because of the orientation level of the packages of graphene layers, vitreous carbon, including RVC, belongs to the group of materials which do not graphitize at high temperature. Type of defects in vitreous carbon structure depends mostly on the choice of precursor material, its preparation and type and method of its processing. In this paper some examples of the most frequently used RVC precursors (e.g. furfuryl resin, phenol-formaldehyde resin) and the methods of RVC preparation starting from the basic framework that is the 100% open-cell polyurethane foam (so called “reticulated foam"). Methods of restructuring the standard commercial polyurethane foam to get the reticulated foam suitable for RVC preparation (i.e. reticulation" methods) are described. The process of impregnation of reticulated foam thus obtained with resins and curing the resulting composite as well as stages of thermal processing leading to carbonization are also discussed. Due to specific properties (high specific surface, thermal and electrical conductivity and good mechanical strength) RVC is presently applied in electrochemistry, medicine or metallurgy. Other forms of vitreous carbons comprise Monolithic Vitreous Carbon (MVC) and Cellular Vitreous Carbon (CVC) — the latter can be applied as sound-absorbing material. Ke[...]
INŻYNIERIA MATERIAŁOWA 1/2016
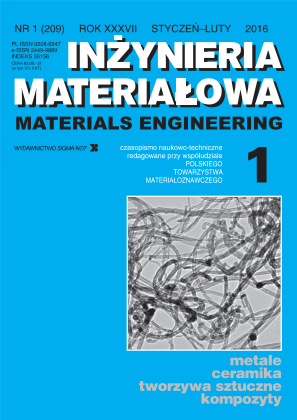
Daria Mikołajczak, Adam Piasecki, Michał Kulka, Natalia Makuch
Laser alloying of 316L steel with boron using CaF2 self-lubricating addition
DOI 10.15199/28.2016.1.1
Abstract
Good resistance to corrosion and oxidation of austenitic 316L steel is well-known. Therefore, this material is often used wherever corrosive media or high temperature are to be expected. However, under conditions of appreciable mechanical wear (adhesive or abrasive), this steel have to characterize by suitable wear protection. The diffusion boronizing can improve the tribological properties of 316L steel. However, the small thickness of diffusion layer causes the limited applications of such a treatment. In this study, instead of diffusion process, the laser boriding was used. The external cylindrical surface of base material was coated by paste including amorphous boron and CaF2 as a self-lubricating addition. Then the surface was remelted by laser beam. TRUMPF TLF 2600 Turbo CO2 laser was used for laser alloying. The microstructure of remelted zone consisted of hard ceramic phases (iron, chromium and nickel borides) located in soft austenite. The layer was uniform in respect of the thickness because of the high overlapping used during the laser treatment (86%). The obtained composite layer was significantly thicker than that-obtained in case of diffusion boriding. The remelted zone was characterized by higher hardness in comparison with the base material. The significant increase in wear resistance of laser-borided layer was observed in comparison with 316L austenitic steel which was laser-alloyed without CaF2. Key words: laser boriding, self-lubricating addition, microstructure, hardness, wear resistance.1. INTRODUCTION AISI 316L austenitic stainless steel is well-known for its good corrosion resistance as well as good resistance to high temperature. It results from a single-phase austenitic microstructure as well as from an effective balance of carbon, chromium, nickel and molybdenum content. Therefore, this steel is often used wherever a high temperature or aggressive corrosive media occur. However, this material is characterized by l[...]
Natalia Makuch, Michał Kulka, Piotr Dziarski
Fracture toughness of gas borided Nimonic 80A alloy
DOI 10.15199/28.2016.1.2
Abstract
Ni-based superalloys are often used in many industrial applications, for example in chemical, petrochemical, aeronautics, nuclear or space industries. These alloys are characterized by a unique combination of low thermal expansion coefficient, high temperature strength, high resistance to oxidation and high corrosion resistance. However, due to their low microhardness and sensitivity to abrasive, erosive and adhesive wear, their application is limited. The boriding process is the appropriate treatment, which will provide high hardness and high wear resistance of Ni-based alloys. Unfortunately, the use of boride layers is limited by their sensibility to cracking under mechanical stresses. Therefore, in this paper the microstructure, microhardness and fracture toughness of gas-borided layer produced on Nimonic 80A alloy were studied. Gas boriding in N2-H2-BCl3 atmosphere was proposed to produce the hard boride layer on Nimonic 80A alloy. This process was carried out at 920°C (1193 K) for 2 hours. The carrier gas consisted of 75 vol.% N2 and 25 vol.% H2. Proposed gas boriding accelerated the diffusion of boron into the surface in comparison with other acceptable diffusion methods. The comparable thickness of boride layer was obtained after considerably shorter duration. Key words: gas boriding, Nimonic 80A alloy, microstructure, hardness, fracture toughness.1. INTRODUCTION Nickel-base superalloys are generally used for application under conditions of high stresses in high temperature, because of their excellent combination of oxidation resistance, corrosion resistance, good stress relaxation resistance and good mechanical properties even at high temperature [1÷3]. However, because of poor wear resistance, the Ni-base alloys under condition of mechanical wear (abrasive or adhesive), require suitable and effective protection. Boronizing is a surface treatment that increases the hardness and wear resistance of metals and their alloys. Generally[...]
Karol Popławski, Beata Kucharska, Elżbieta Jezierska, Jerzy R. Sobiecki
Microstructure studies of nickel-carbon nanotubes nanocomposite coatings formed by electrodeposition
DOI 10.15199/28.2016.1.3
Abstract
Many researchers nowadays concentrate on nanocrystalline metal-matrix composites, as well as on composites reinforced by nanoparticles, to find more suited materials to be used in aviation, nuclear power plants or as a hydrogen storage for fuel cells. The aim of this paper was to investigate the possibility of producing nanocrystalline nickel-based composite coatings reinforced by carbon nanotubes (Ni-CNT). The goal was to obtain well immersed carbon nanotubes fully dispersed in nanocrystalline nickel matrix by using standard electrochemical deposition equipment and modify the process by changing parameters like bath composition, additives, nanotubes content or stirring method. The effect of optimization of these parameters on composite’s microstructure, surface topography and nanohardness was investigated. Also, usefulness of different approach, so called “stirring electrode" was examined. Scanning electron microscopy, transmission electron microscopy with electron diffraction, X-ray diffraction and Raman spectroscopy were used to determine the microstructure of obtained coatings. Key words: nickel nanocomposite, carbon nanotubes, metal-matrix composite, microstructure, nanohardness.1. INTRODUCTION Many researchers are now focusing on the development of the composites with nanocrystalline metal matrix and composites reinforced by the nanoparticles [1÷3]. Since the discovery of carbon nanotubes [4] an intensive work has been done in attempt to exploit their properties, and tries has been made to include them as a reinforcement of nanocomposites [5÷7]. Composites like that are used in aerospace, nuclear energy and as the storage of hydrogen in fuel cells [5]. An example of such a material is a nanocrystalline nickel matrix based nanocomposite reinforced by carbon nanotubes (Ni/CNTs). They are currently attempts to produce this type of material in the form of geometric solids with significant volumes, such as a few millimeters[...]
Joanna Piwowarczyk, Roman Jędrzejewski, Jolanta Baranowska
Influence of atmosphere composition on the structure and properties of aluminum oxynitride coatings deposited by PLD method
DOI 10.15199/28.2016.1.4
Abstract
This work presents studies on the influence of oxygen content in reaction atmosphere during pulsed laser deposition on the structure and properties of aluminium oxynitride films. The coatings were grown on monocrystalline Si substrates. Aluminium nitride bulk disk was used as a target. The film deposition took place at room temperature and pressure of 0.5 Pa with varying content of oxygen and nitrogen. Thickness and roughness of the coatings were measured by profilometer. The X-ray diffractometer (XRD) was used for phase analysis of the coatings. Chemical composition was evaluated using X-ray microanalysis (EDS) by means of scanning electron microscopy (SEM). The surface topography was examined using an atomic force microscopy (AFM). Hardness of the coatings was measured by means of nanoindentation. Adhesion was evaluated in microscratch tests and the morphology of the residual scratch was characterized by AFM. Results showed that it was possible to obtain coatings composed of oxynitrides with different stoichiometry. Mechanical properties of the obtained coatings, however, were significantly different from those demonstrated by ALON ceramic. The content of oxygen in the coatings had an influence on the decreasing hardness and Young’s modulus and improved adhesion. There was no influence on thickness and roughness but the lowest number of droplets was noticed in the coatings obtained in pure oxygen. Key words: aluminum oxynitride, thin ceramic film, pulsed laser deposition.1. INTRODUCTION Aluminum oxynitride ceramic, acronym ALON, has been focusing interest since the 1960s [1÷3]. It has a cubic crystal structure with a spinel-type lattice (space group: Fd3m) [3÷6]. Its general chemical composition is Al(64 + x)/3O32 - xNx, where 0 ≤ x ≤ 8 [7, 8]. The most stable and stoichiometric phase is represented by Al23O27N5 (when x = 5) [1]. ALON has excellent mechanical properties with high strength and high hardness [1, 3, 9] be[...]
Kazimierz J. Ducki
The characteristic of deformability of Fe–Ni superalloy during high-temperature deformation
DOI 10.15199/28.2016.1.5
Abstract
The influence of two variants of initial soaking at 1100°C/2 h and 1150°C/2 h and parameters of hot plastic deformation on the deformability of Fe-Ni superalloy have been presented. The hot deformation characteristics of alloy were investigated by hot torsion tests using Setaram torsion plastometer. The tests were executed at constant strain rates of 0.1 and 1.0 s-1, and testing temperature in the range of 900 to 1150°C and were conducted until total fracture of the samples. Plastic properties of the alloy were characterized by worked out flow curves and the temperature relationships of maximum yield stresses (σpp) and strain limits (εf). The flow stress of the torsion tests showed a single peak in the flow stress-strain curves, and indicated that a dynamic recovery and recrystallization took place during the hot deformation. It was found that optimal values of flow stresses and strain limits were obtained for the alloy after its initial soaking at 1100°C/2 h and deformation in the temperature range of 1050÷950°C at strain rate 0.1 s-1. The increase of maximum yield stresses, σpp, and decrease of strain limit of the alloy, εf, as the initial soaking temperature was rising up to 1150°C/2 h, with the strain rate increasing to 1.0 s-1, was associated with a growth of the initial grain size and the degree of austenite saturation with alloying elements. The relationship between the maximum yield stresses and the Zener-Hollomon parameter (Z) was described by σpp = A × Zn power function. Activation energy for hot working (Q) was assessed for the alloy after two variants of initial soaking, i.e. 1100°C/2 h and 1150°C/2 h and amounted, respectively, 442 kJ/mol and 519 kJ/mol. Key words: A-286 superalloy, hot deformation, plastic properties, Zener-Holomon parameter, activation energy for hot working.1. INTRODUCTION The behaviour of metals and alloys during hot plastic working has a complex nature and it varies with the changing [...]
Tomasz Pawlik, Daniel Michalik, Małgorzata Sopicka-Lizer, Radosław Lisiecki
Effect of AlF3 and H3BO3 fluxes on the structure and optical properties of Ca-α-SiAlON:Eu2+ phosphor powders
DOI 10.15199/28.2016.1.6
Abstract
The continuous increase in demand for electric power necessitates constant search for new energy-efficient and economical light sources. One of them are light-emitting diodes (LEDs), requiring further development of materials enabling generation of warm white light that could replace the conventional light sources used so far. Problems related to the use of white LEDs include relatively low efficiency and light quality. A material that is currently a subject of interest due to its optical properties is Eu2+ doped Ca-α-SiAlON. It is regarded as one of the materials that can potentially be used as a yellow phosphor in white LEDs. The broad emission spectrum of Ca-α-SiAlON:Eu2+, bearing similarities with YAG:Ce3+ emission, is characterized by an emission peak maximum located in the wavelength range of 570÷585 nm, which enables obtaining a high colour temperature of a white LED. This study investigates the effect of addition of 1÷5 wt % AlF3 and H3BO3 as fluxes on the optical properties of phosphors obtained at different temperature. The syntheses were conducted in the temperature range of 1450÷1650°C in an N2/CO atmosphere. On the basis of the examination of the powder phase composition (by XRD), morphology, and chemical composition in microareas (by SEM/EDS), and the comparison of the emission spectra of the Ca-α-SiAlON:Eu2+ powders with a different flux content, it was found that the addition of AlF3 had a positive effect on emission intensity and quality. Key words: phosphors, wLED, sialon, flux, optical properties.1. INTRODUCTION Practically since the invention of the light bulb by Thomas Alva Edison in 1879 and the replacement of the steam engine with the first electric engines in industrial applications, a continuous increase in electric power consumption has been observed. Even at that time Edison realized the significance of his invention and he initiated the establishment of the first public power plant in the world in[...]